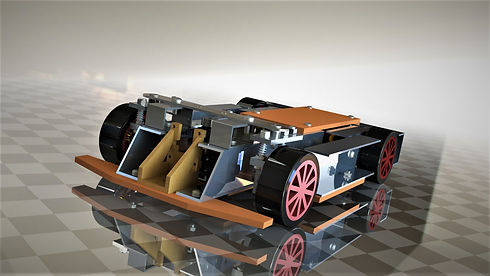
RC Car
To simulate the "fast and furious" of car racing
Late 2016
Need for Speed was once my favorite game, and I had been hoping to experience the same "fast and furious" in real life. The RC car is a project that can simulate the fast and furious of car racing, without putting the driver in danger. The idea is to design an RC car with an FPV system.
First attempt
A huge failure
Overall structure
The 775 motor does not run well on the scooter, however, it should run on an RC since it is much lighter, so I decided to use 775 again as I have it already. The problem now is the suspension. However, the traditional car suspension did not look easy to me at that time, so I came up with the idea of splitting the car body into three components and having the suspension connecting the components.

Splitted body
The car consists of a front deck, a back deck, and the main body. The back and front decks are connected to the main body with hinge and springs. The rotational degree of freedom around the y-axis would form a suspension system.

Steering
The best way to steer an RC car is obviously using a servo, so I went ahead and designed a parallelogram steering mechanism for the car. Since the front wheel is neither powered or suspended, there is not much to concern.
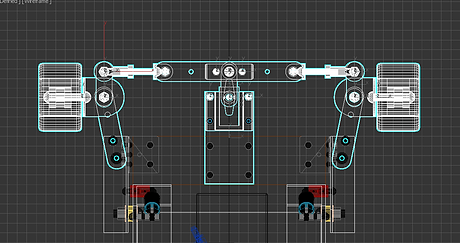.png)
Ridiculous selection of CAD software
Perhaps you have already noticed, the CAD is done in 3ds Max! Yes, I used an animation design software to do engineering drawings. The only reason that I did that is because I used to use 3dsMax to make models for 3D printing. It was definitely a bad practice and this soon became my last use of 3dsMax.
.png)
Now presenting, the ultimate trash
This is the prototype that I made after struggling for one month. However, it is a complete piece of trash. The 775 motor was heavy and inefficient and the skateboard tires had terrible traction, let alone the terrible look of the car. The ESC is so bad that it generates more sparks in the motors than power when driving two motors, and that caused me to remove one of the motors. Soon, I got the car crashed and decided to restart.
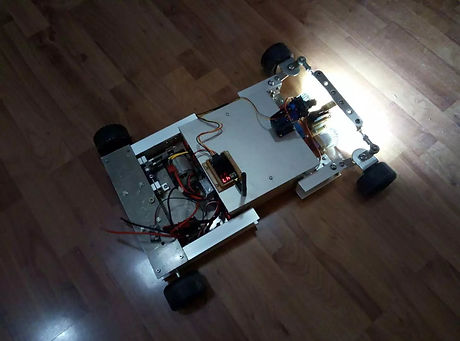
Redesign
Learn from mistake
The problem of the first RC includes: heavy, oversizing, inefficient motor and ESC, ineffective suspension and poor impact protection.
​
Overall structure
This time, I decided to give up the three components design and switched to the more traditional one. To prevent the same weight and oversizing problem from happening again, I decided to limit the width of the vehicle to 20cm. Feeling desperate for the skateboard wheels, I bought tires for RC cars. In addition, I decided to use Solidworks for CAD which I just learned from the Robot Club this time.

Front deck
Since the overall structure is changed, I had to redesign the suspension. I found the SK10 shaft support a perfect hub for the front wheel, so I decided to design a suspension based on that. The idea I had is to tighten two screws on the SK10, put spring around the screws and let them go through the holes on another plate at above. The plates then become prismatic joints that allow movement of the wheel hubs in the z-axis.
.png)
Steering
Same as the last time, I designed a parallelogram steering mechanism for the car. The plates that connect the wheel hubs with prismatic joints are connected to the car with hinges and are powered by the servo. Last time, the steering system got crashed because of a lack of protection, so I decided to put a replaceable bumper in front of the car that protects the steering system.
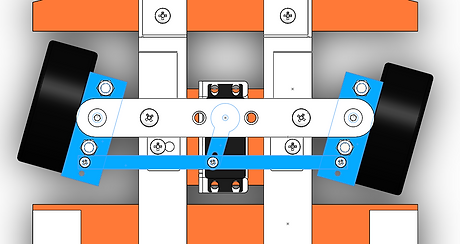.png)
Back deck
I replaced the 775 motors with two 930kv A2212 brushless motors that are much more efficient. I made each motor power one rear-wheel so that a differential is not needed. The belt drive has a gear ratio of 5:2 to provide a theoretical speed of 2/5*12.6V*930RPM/V*0.065m*pi/(60s/min)*3.6kph/mps = 57.4kph. The spring is for suspension purposes.
.png)
Overall distribution of components
All the critical designs are completed, so the rest is putting everything in the box. Because there was so much interference to avoid, I spent another two months to finish the CAD.

The product
At long last, from December 2016 to March 2017
CAD
![]() Rendered picture | ![]() Top view | ![]() Left view |
---|
Product
![]() The car | ![]() FPV | ![]() Motors and transmissionThe reason that the output shafts are so long is that at first the coupler that I used to connect the motor to the belt wheel extended the length and put the belt wheel 18mm from the motor, but soon I found that a high deflection of shaft would occur at high torque, making the belt not in good contact with the belt wheel. Then I replaced the original coupler with one that minimizes the extension, but I did not bother to cut the output shafts. |
---|---|---|
![]() Front LEDLater added, controlled by Arduino Nano | ![]() Left view | ![]() The frontThe camera support was soon designed to provide better protection. |
Running
The car runs at a maximum speed of 50kph.
Control and coding
The servo and ESCs are connected to the 2.4GHz receiver directly and the control program is preset. The left joystick on the remote control is the throttle and the right joystick on the remote-control controls steering. The only modification I made is the light, which is controlled by an Arduino Nano. The Arduino Nano reads the Channel 5 signal from the receiver and adjusts the light accordingly. The On and Off of Channel 5 is controlled by a button on the remote control.
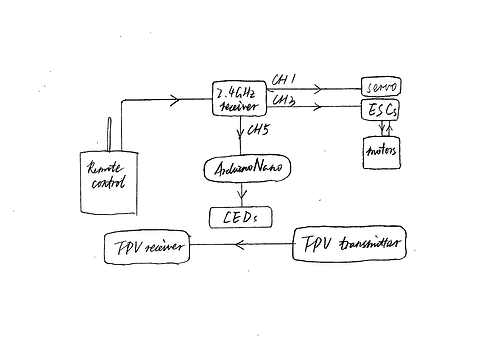

Retrospect
This car lasted really long, it still runs perfectly today. In fact, I still made several changes to it a year after completion. The biggest one was replacing the parallelogram-steering with trapezoidal steering to increase the steering efficiency. However, the suspension design is really not effective, and the exposure of cable and components to the outside is also not a good engineering practice. Because of these defects, I had planned to design a completely upgraded version of RC Car.
This RC Car is really the first mechatronic project completely done by myself. You can probably tell that I really tried not to search for anything online but instead came up with my own design. Such an approach is definitely inefficient for fast product development, however, it made me learned from mistakes and made me more creative. Besides, who says that the traditional designs that have been around for tens of years are the best?